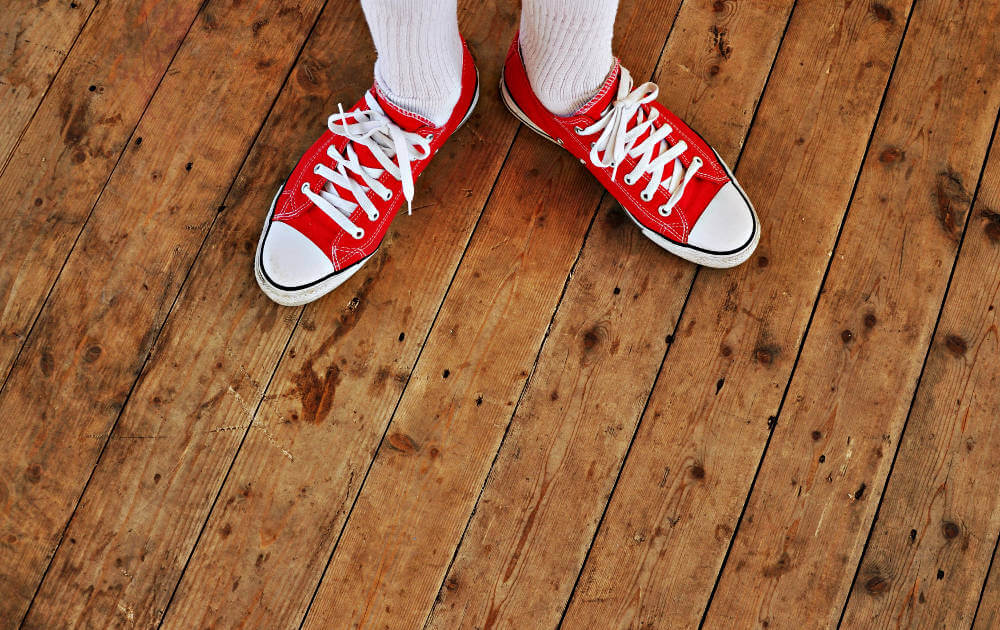
28 Feb Starting from a clean base
When laying new flooring, perhaps the most important element of the job is making sure that the subfloor is clean and dry before you even think about getting started with the addition of new flooring materials. While there are certain requirements for some materials – and we will explore these here as well – there is one common theme in subfloor preparation: starting from a clean base. This month we take a look at what this means and how it can be achieved in order to give your new floor a flawless look that will last for longer.
As well as removing old flooring, such as carpets, carpet tiles, vinyl tiles, wood plank, etc., your contractor will also ensure that this includes everything that was used to lay that flooring in the first place. After removing the old flooring, the next step is to remove any old nails or staples. That’s the easy part! Next comes making sure that old adhesives and sealants are removed as well. There are two kinds of adhesive: thick and hard or soft and sticky.
For the thicker, harder adhesives, this is fairly straightforward and can be done with a planing machine. Softer and stickier materials tend to soften with the heat of a planing machine though, making them stick even more to a surface and harder to remove. For those, a grinding machine is usually more suitable and will get the job done. It helps to know what sort of materials you are dealing with first in order to have the right equipment to hand, although it’s not always possible. Your contractor should be able to help in most instances as particular types of flooring materials will require specific adhesives and sealants in order to be properly fixed in place. Where it is not feasible to fully remove old adhesives, it is possible to apply a suppressing primer and smoothing compound which will ensure that they will not interact with the new materials being placed on top of them.
If your building was constructed before 1968 asbestos may be present in your flooring – either in cement, if that was used, or in the adhesives themselves as it was a widely-used material for a number of flooring types. If this is the case, or if you suspect asbestos may be present, be sure to inform your flooring contractor as specialist equipment will need to be used for both their and your safety.
Once all external materials have been removed, the next step is to check for cracks and holes and to secure any loose floorboards. Repair mortar can be used to fill any cracks and holes allowing enough time for this to dry before moving on to the next steps. Moisture content is critical for many flooring types and particularly for concrete subfloors. The moisture content of cement should not be above 75%. In instances where there not enough time to allow for proper drying, it is possible to install a damp-proof membrane to prevent moisture from rising and lifting or warping your new flooring.
For advice and professional subfloor preparation services, our team of specialists at Easifit Flooring is on hand to help. You can get in touch with us by phone on 0800 096 1171 or email us on for a chat or for your free quote.
February 28, 2018